John Rannoch Foods 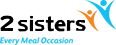
Armagard Fournit À John Rannoch Foods Limited La Capture De Données En Atelier.
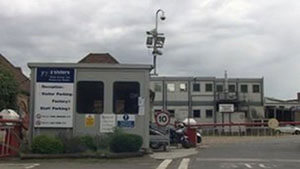
À Propos de John Rannoch Foods Limited
Avec des locaux situés sur 200 acres de parc à Haughey Park près de Stowmarket, Suffolk, John Rannoch Foods Limited - une partie du 2 Sisters Food Group - est spécialisé dans la transformation de la volaille.
L'entreprise privée indépendante est un fournisseur majeur de Marks and Spencer et d'autres grands détaillants, dont Whitbread. John Rannoch exploite sa propre flotte de transport avec une vingtaine de livraisons par jour, avec des véhicules faisant la navette entre l'usine et les centres de distribution régionaux des clients.
Le Défi
John Rannoch Foods souhaitait moderniser ses processus manuels de distribution et d’enregistrement des données, qui impliquaient beaucoup de paperasse, dans l’ensemble de son réseau d’usines. Pour ce faire, l’entreprise souhaitait installer des systèmes informatiques dans l’atelier, mais ce n’était pas une tâche facile dans un environnement aussi impitoyable qu’une usine de transformation de viande.
Ils avaient besoin d'une solution capable de résister à des conditions humides et mouillées. De plus, en tant qu'usine de production alimentaire, toute solution devait être facile à nettoyer afin de maintenir les normes d'hygiène.
La Solution

John Rannoch Foods a choisi d'installer 35 terminaux Armagard dans ses installations. Chaque terminal est logé dans un boîtier en acier inoxydable, conçu spécifiquement pour répondre à la spécification IP67 pour les environnements hostiles et humides.
Un boîtier séparé est utilisé pour abriter une imprimante pour étiquettes à codes-barres, ce qui permet à John Rannoch Foods d'utiliser n'importe quelle imprimante d'étiquettes grand public du marché.
Paul Nix, responsable des systèmes d'information de John Rannoch Foods, a déclaré : « En gardant cette option ouverte, nous avons pu rechercher des imprimantes adaptées mais moins chères dans le commerce. Nous avons des unités de rechange en stock et elles sont faciles à remplacer sans mettre le terminal hors service. »
Les étiquettes à codes-barres sont un élément essentiel du système de contrôle de production de John Rannoch et la majorité des terminaux PC sont équipés de scanners laser à codes-barres Armagard.
Les Résultats
Chaque article entrant et sortant de l'usine est désormais facilement enregistré, soit en scannant l'étiquette à code-barres pour l'identification, soit en imprimant une nouvelle étiquette pour confirmer l'achèvement d'un processus de production.
Le code-barres assure la traçabilité de chaque produit et ingrédient expédié par l'usine, ainsi que les numéros de référence de la commande et les dates de traitement.
Les terminaux informatiques nouvellement installés jouent un rôle important dans la planification des commandes, la définition des priorités et l'approvisionnement en matières premières. Historiquement, cela impliquait un niveau élevé de travail manuel pour l'impression et la distribution des plannings informatiques et la réalisation manuelle des enregistrements pour chaque processus de lot.
Les terminaux informatiques sont utilisés pour présenter le planning de production à chaque poste de travail. Au lieu de devoir enregistrer manuellement les articles qu'ils ont utilisés, les employés peuvent scanner les informations figurant sur l'étiquette à code-barres.
De même, au lieu d’enregistrer ce qu’ils ont fabriqué, ils impriment une étiquette et la collent sur l’objet pour transmettre l’information via le système.
Retour sur Investissement
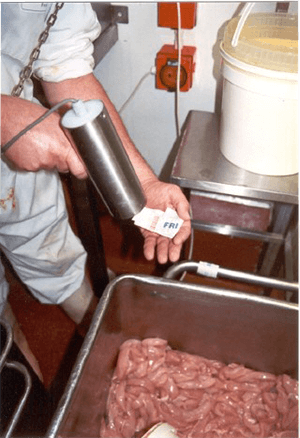
Paul Nix estime que les terminaux informatiques permettent à l'entreprise d'économiser environ 2 % sur les coûts de main-d'œuvre. Avec un effectif total de 1 000 personnes, cela équivaut à 385 000 € (£330 000) à 585 000 € (£500 000) par an.
« Concrètement, cela signifie que nous avons obtenu un retour sur investissement positif, récupérant le coût du matériel en moins de neuf mois », a déclaré Paul Nix.
Le traitement de chaque commande client prend jusqu'à 48 heures pour la livraison des produits finis. Le processus comprend environ 8 à 10 étapes, de l'abattage du poulet à la découpe, l'assaisonnement, la cuisson, l'emballage et l'expédition.
Paul Nix a déclaré : « Nous évoluons dans un marché très dynamique où les besoins en commandes peuvent changer quotidiennement. Étant donné que tous nos produits et les ingrédients que nous utilisons, comme la crème, ont une durée de conservation limitée, il est essentiel que nous ayons une visibilité complète sur l’état de notre production afin de contrôler les stocks et l’approvisionnement en matériaux. »
« Le nouveau système nous permet de minimiser les déchets, de déployer notre main-d'œuvre plus efficacement et, par conséquent, de répondre plus efficacement aux commandes de nos clients », a ajouté M. Nix.
Moins D'erreurs Et Moins De Déchets
Depuis l’installation des nouveaux terminaux informatiques, John Rannoch Limited a mis en place un processus plus efficace pour l’approvisionnement en matières premières. M. Nix a commenté : « Comme nous faisons moins d’erreurs, notre consommation de stock a diminué de 80 palettes au cours des trois derniers mois. »
« Nous avons également constaté une réduction correspondante des déchets. Traditionnellement, les déchets nous coûtaient environ 5 % du chiffre d’affaires. Les déchets se présentent sous différentes formes, comme la livraison excessive au client ou l’élimination de matériaux excédentaires résultant d’une commande excessive d’ingrédients clés », a déclaré M. Nix.